By using some sort of power electronics (like variable frequency drive) to adjust the line frequency seen by the asynchronous motor, rather than having a dedicated rotating supply capable of producing a variable frequency output.
Although VFDs can be used to limit inrush and act as a "starter", the true soft starter is often a much better choice when considering cost and robustness of the system. VFDs only make a difference when they are employed continuously in the process to vary speed in an effort to optimize overall system performance and energy usage.
This shows how complex a VFD can be if you do not understand the Inverter process. Several questions have to be answered before determining what could be possible causes for motor overheating. What load is the motor running at with the low frequency? Do you have VFD drive curves that show how the drive reacts to differing loads at low frequency? Do you have access to the firmware control diagrams that shows how the fault is generated?
How to address this depends upon your process.
1) You can do the theoretical math with some software on the internet;
2) you could do a before and after measurements and
3) adjust the process.
1) You can do the theoretical math with some software on the internet;
2) you could do a before and after measurements and
3) adjust the process.
If you have a VFD (variable frequency drive) with no input phase loss detection, it allows you to use the VFD as a phase converter because it will just rectify the line to DC, then recreates the pseudo AC on the output as 3 phase. When you do this, the VFD needs additional capacitance to smooth the extra ripple from not having a 3 phase rectifier bridge, use the bridge diodes must be sized to handle all of the power at the single phase current, 1.732 times more.
I have a 50 HP drive suitable for variable torque application. Can I use the same drive for a 50HP load, but on a constant torque application? Or do I need to up size or downsize these drives? What is the turndown ratio I need to calculate and how will I get it?
For most of the smaller VFDs on the market today, the harmonics are dealt with internally in the unit. The question of the level of harmonics expected is definitely not a simple one. There are many factors from the transformer size and utilization, cable length, other harmonic producers on the network.....etc !!
Voltage drop along the cable will reduce the actual starting current. If we for example choose 25mm2 cable, we would have around 9% voltage drop at nominal load, over the 400m cable length.
One benefit of IGBTs is that they can be designed to survive a direct short-circuit across the bus, for several microseconds (Short Circuit SOA capability), versus Superjunction FETs do not have this capability.
Few manufacturers make a VFD with simple programming. It is easy to code in a so much application specific capabilities in the chips coming out now. So much room with little cost you may as well fill it up!
In my experience at Vacon Drives, the STO card has a double contact on their to be sure that the power stage is disabled. Much like having two contacts on e-stop, but now two relays to disengage the power, just in case one gets stuck. The Safe Stop 1 (SS1) safety function consists of two safety related subsystems, an external time delayed safety relay and the STO safety function. These two subsystems combined compose the Safe Stop 1 safety function. Contrary to popular belief this is a programmable input in the manor that the action of the STO is programmable.
There are about 6 different causes of shaft currents in Variable Frequency Drive driven motors. I can't remember them all but some are:- high DV/Dt, phase unbalance - shift in theoretical neutral point (poor inverter and lack of filtering), capacitive coupling. Many manufacturers recommend insulating the non-drive end bearing and installing carbon brush on the drive-end.
Category
AC Motor Control
Featured
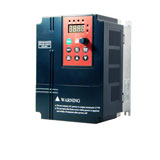
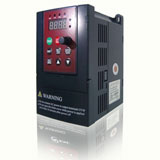
Recent
Increase the speed of a motor by VFD
VFD in Crane and Hoist Applications
VFD for Fire Pump Motors
Is it VFD the best solution to control pump?
3HP VFD, single phase to three phase VFD
Insulated bearings for electric machines
Control ABB VFD through RTD 250ohm directly on water temp
Variable frequency drive Preventive Maintenance
Large VFD trips with power supply by transformer
Induction motor power factor
Understanding VFD basics
Does the motor lifetime depend on the starts number & frequency?
VFD in Crane and Hoist Applications
VFD for Fire Pump Motors
Is it VFD the best solution to control pump?
3HP VFD, single phase to three phase VFD
Insulated bearings for electric machines
Control ABB VFD through RTD 250ohm directly on water temp
Variable frequency drive Preventive Maintenance
Large VFD trips with power supply by transformer
Induction motor power factor
Understanding VFD basics
Does the motor lifetime depend on the starts number & frequency?