Another example that springs to mind is controlling variable frequency drives on a databus. The VFD manufacturers usually organize the control using a command word and a status word. Individual Boolean signals can be accessed if required, but sometimes you can handle that data efficiently at the word level using bit shifts and masking. There may, for example, be a series of bits identifying different faults, but if they are allocated contiguously, which you would usually expect them to be, it might be more efficient to create a general 'fault' signal using masking and bit shifting rather than Anding all the individual fault bits.
As maintenance engineer in a sugar factory, I have been having problem with induction motor 37Kw driven by variable frequency drive (VFD), type Vacon NXS, this motor is running normally at 1200 rpm with draw current about 8.5A, the thing is that this motor was stopped working the drive HMI shown "Saturation Trip" which was indicating the drive is gone, we changed the drive & fuses with a new one and the motor restarted.
Simply put, a variable frequency drive can save energy COMPARED to OTHER means of VARYING flow and/or pressure in centrifugal machines, like pumps and fans. If you are not VARYING the speed, you will not save energy, regardless of whether is full speed or not. There are more cost effective means of permanently CHANGING the output if it will run continuously at that output. But if VARYING the speed is a part of your process (the work that the machine does), then compared to OTHER methods of accomplishing that, a VFD will save significant energy. This is a very commonly misunderstood and overstated part of the picture.
Using variable frequency drive (VFD) for the servo application is quite possible, provided the application is less demanding in critical positioning purpose.
Servo motors have different information on motor control, it includes rotor positioning feedback, VECTOR mode, requires motor recognition and not necessary and encoder for rotor feedback, it estimates it through output current. (which includes V/F also) Numerical Commands can set V/F setpoint on power modules usually.
A VFD (or VSD) can operate down to its minimum designed frequency, however the motor design and load characteristics determine the minimum PRACTICAL frequency. If the motor is force cooled and the variable frequency drive is operated in vector mode, as long as there is encoder feedback, and the load is not excessive, it is possible to achieve 100% torque at zero frequency.
Modern PWM frequency drive was first developed in Stromberg Finland early 1960s. First commercial break through was Helsinki metro at 1972. This development was lead by Martti Harmoinen. They also developed first commercial cyclo converter in 80s and many other pioneering innovations.
Category
AC Motor Control
Featured
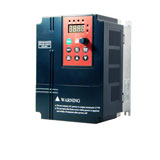
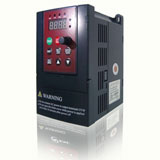
Recent
Increase the speed of a motor by VFD
VFD in Crane and Hoist Applications
VFD for Fire Pump Motors
Is it VFD the best solution to control pump?
3HP VFD, single phase to three phase VFD
Insulated bearings for electric machines
Control ABB VFD through RTD 250ohm directly on water temp
Variable frequency drive Preventive Maintenance
Large VFD trips with power supply by transformer
Induction motor power factor
Understanding VFD basics
Does the motor lifetime depend on the starts number & frequency?
VFD in Crane and Hoist Applications
VFD for Fire Pump Motors
Is it VFD the best solution to control pump?
3HP VFD, single phase to three phase VFD
Insulated bearings for electric machines
Control ABB VFD through RTD 250ohm directly on water temp
Variable frequency drive Preventive Maintenance
Large VFD trips with power supply by transformer
Induction motor power factor
Understanding VFD basics
Does the motor lifetime depend on the starts number & frequency?