HomeDefinitionPage 2
A standard VFD starts with reduced voltage and frequency and operates with a constant ratio of voltage to frequency as the frequency increases. This maintains the motor at its full load current rating for a constant torque load. With variable torque loads - fans/pumps - the current is low at low frequency rising to the motor's full load current rating at rated frequency.
Variable frequency drive comes in a lead role for energy saving products for the all industries using electrical motors. Main function of VFD is to vary the speed of the AC motor as per requirement and for some application provide high torque. But main problem come with all VFD drives is harmonics, industries which are using large no. of VFDs and other power electronics devises face too much problem of harmonics.
Sensorless Vector Control is included in nearly all VFD manufacturers offerings. The difficulty remains in maintaining 100 Torque at Zero Speed and the truth is that very few can accomplish that standard of performance. As the title of the type of control suggests, the typical control scheme involves measurement of the opposing fields vectors, and this gets very difficult to do when you minimize the field to reach zero speed.
If you've not yet had the opportunity, check out an ABB drive utilizing DTC (Direct Torque Control) with a properly Autotuned VFD capable Motor, you can achieve Torque control at Zero speed. As for PM motor control, the complexity is high, yet we have accomplished very good control with Resolver feedback for Pole alignment, adequate cooling, and alternative bearing types at extended HP and RPM levels. Todays processor and power module technology is enabling what has until now not been possible.
Bearing currents come in several different appearances. However, while modern motor design and manufacturing practices have nearly eliminated the low frequency bearing currents induced by the asymmetry of the motor, the rapid switching in modern variable frequency drive systems may generate high frequency current pulses through the bearings.
The acceleration time should be enough time for the motor and connected load to achieve set operating speed without causing the motor or connected load any additional wear and tear. This is the soft-starting ability of the VFD.
Shaft voltage is not produced by the harmonic voltages and currents in the stator windings being supplied from a VFD; however, for VFDs with high frequency PWM carriers, the distributed capacitance will look like a low impedance pathway and can produce a greater shaft voltage than that produced in a similar direct drive machine. It is important to note that shaft voltage can be produced in non-VFD applications as well as in DC machines and has been observed in both motor and generator applications.
A VFD (variable frequency drive) is generally used to control a squirrel cage type motor, where both stator and rotor are of a wound type to create the magnetic flux. Servo drives are used to control permanent magnet motors. Permanent magnet motor because they use rare earth magnets in the rotor, create a much higher magnetic flux for their given size. This enables the motor to be able to create more torque in a much smaller rotor and hence motor size. Giving the motor a lower inertia to accelerate and decelerate much more dynamically than that of the asynchronous squirrel cage type motor.
The SAFE TORQUE OFF function provides a means for preventing the variable frequency drive from generating torque in the motor, with a very high level of integrity. It is suitable for incorporation into a safety system for a machine. It is also suitable for use as a conventional drive enable input. The safety function is active when the STO input is in the logic-low state as specified in the control terminal specification. The function is defined according to EN 61800-5-2 and IEC 61800-5-2.
VFD (variable frequency drive) technology enables centrifugal machines to operate at off design conditions at 0.50, 0.40 and even at 0.30 kW/ton. As the cooling load decreases, the VFD decreases its output voltage/ frequency, slowing chiller. The result the chiller operates at near full load efficiency for almost the entire operating range and allows the chiller to operate as low as 10% of rated output without experiencing surging.
There are 3 types of control schemes for VFDs, V/Hz, Vector and Flux. Most major VFD vendors like Danfoss, ABB, Rockwell Automation, all have each technology. V/Hz is the oldest, most basic control scheme but is still used by all VFD vendors for multiple motor applications. Vector technology offers enhanced control and the ability to control a motor closer to 0 speed (V/Hz is limited to ~ 5 Hz as a minimum usually). Flux control is the highest level and can match DC performance such as full torque at 0 speed. Many variable frequency drive companies have flux capability like Danfoss and ABB. ABB's version of flux control is DTC.
Generally, there are dozens of function parameters in variable frequency drive (VFD), or even hundreds for option. In practical application, it is not necessary to set every parameter, most parameters can be keep factory default settings.
Category
AC Motor Control
Featured
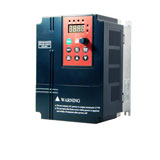
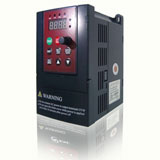
Recent
Increase the speed of a motor by VFD
VFD in Crane and Hoist Applications
VFD for Fire Pump Motors
Is it VFD the best solution to control pump?
3HP VFD, single phase to three phase VFD
Insulated bearings for electric machines
Control ABB VFD through RTD 250ohm directly on water temp
Variable frequency drive Preventive Maintenance
Large VFD trips with power supply by transformer
Induction motor power factor
Understanding VFD basics
Does the motor lifetime depend on the starts number & frequency?
VFD in Crane and Hoist Applications
VFD for Fire Pump Motors
Is it VFD the best solution to control pump?
3HP VFD, single phase to three phase VFD
Insulated bearings for electric machines
Control ABB VFD through RTD 250ohm directly on water temp
Variable frequency drive Preventive Maintenance
Large VFD trips with power supply by transformer
Induction motor power factor
Understanding VFD basics
Does the motor lifetime depend on the starts number & frequency?